As we all know, the printing of cigarette packets is mainly gravure printing, while the traditional gravure printing uses solvent-based inks, which is the "culprit" of the residual solvent of cigarette packets. The water-based ink uses water as the main solvent and water-based ink instead of solvent-based ink. It can effectively solve the problem of high residual solvent content of cigarette packets.
In the following, taking a cigarette package product of the author company as an example, the application of gravure aqueous ink in the field of cigarette package printing is discussed.
Process improvement program
The printing scheme of the cigarette packet box product is: 4-color pattern + 2-color solid spot color + glazing (as shown in Fig. 1). Among them, the spot color part of the field accounts for about 90% of the total area of ​​the product, and it is printed with water-based ink; the 4-color pattern is still printed with solvent-based ink.
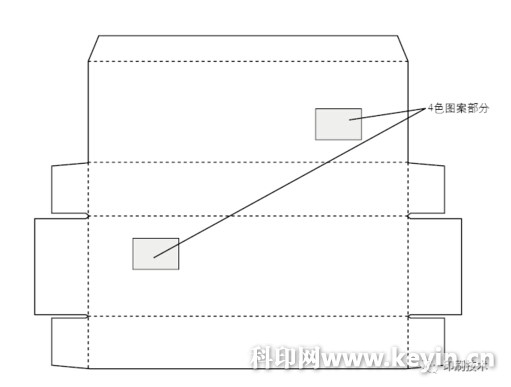
The purpose of this process improvement is to solve the problem of high solvent residue in the cigarette packet box product. In view of the disadvantages of slow drying speed and poor leveling in the ground, compared with solvent-based inks, the ratio of the first to the first is The larger area of ​​the spot color section was improved.
Process adjustment
In view of the two shortcomings of slow drying speed of water-based ink and poor leveling in the field, our company has adjusted the process as follows.
1. Slow drying speed
Drying performance is one of the main indicators of water-based inks. The drying speed of the aqueous ink is slower than that of the solvent-based ink, and once the drying is insufficient, an ink sticking phenomenon occurs. The solution is as follows:
When the printing speed is kept unchanged at 156 m/min, the drying temperature is raised from the original 52 ° C to 62 ° C;
Change to the shallow net, the depth of the gravure cell is changed from the original 53μm to 43μm.
After the above process adjustment, the drying performance of the aqueous ink has been improved to some extent.
2. Poor leveling in the field
Water-based inks use water as the main solvent, but the surface tension of water is large, which makes the wetting of the printing materials and pigments difficult, resulting in poor leveling of the final printed products. The solution is as follows:
Ink suppliers cooperate with our company to carry out relevant tests, adjust the formulation of water-based inks, reduce the surface tension of water-based inks, and enable the water-based inks to fully wet and level on the paper surface, and transfer them more evenly;
Adjust the ratio of water to ethanol, increase the viscosity of water-based ink and strictly control the viscosity change, increase the oven temperature, increase the amount of blowing, and ensure that the water-based ink is dry thoroughly;
In the gravure process, a new amount of ink is added in a small number of ways to ensure the stability of the pH of the aqueous ink.
Comparison of indicators before and after improvement
1. Comparison of solvent residues
Ten samples of cigarette packs before and after the improvement were randomly selected and tested according to YC/T 207-2014 "Determination of Solvent Residues in Tobacco Paper by Headspace-Gas Chromatography/Mass Spectrometry". The solvent residue comparison is shown in Table 1.
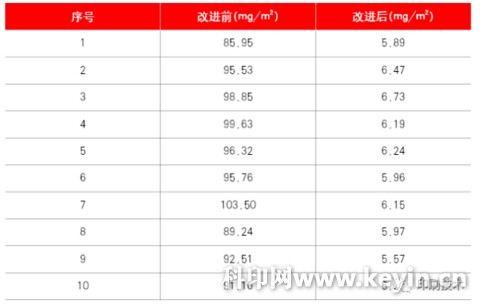
It can be seen from Table 1 that the residual amount of the tobacco packet solvent after the process improvement is significantly reduced, which effectively solves the problem of high solvent residue of the cigarette packet box product.
Cheapest Diapers,Best Baby Diapers,Baby Diapers Online,Disposable Baby Diapers
Shandong Tianzige International Trade Co., Ltd , https://www.sdbabydiapers.com