[Introduction] Abstract: The electrospinning process is a method for directly and continuously preparing polymer nanofibers, which has the advantages of simple process, convenient operation and fast manufacturing speed.
Foshan Lezi Precision Measurement and Control Technology Co., Ltd. 528225
Abstract: The electrospinning process is a method for directly and continuously preparing polymer nanofibers. It has the advantages of simple process, convenient operation and fast manufacturing speed. It is widely used in medical and environmental protection fields. The research progress of electrospinning technology and its application in recent years is introduced. The principle and influencing factors of electrospinning are reviewed. The future application of electrospinning technology is prospected.
Key words: electrospinning; nanofibers; progress
introduction
Nanofibers are strictly referred to as ultrafine fibers having a fiber diameter of less than 100 nm. It has the characteristics of large specific surface area and high porosity, so it can be widely used in high-efficiency filter materials, biological materials, high-precision instruments, protective materials, nanocomposites and other fields. The warming of nanotechnology research in the 1990s made the preparation of nanofibers a hot research topic. The electrospinning preparation of polymer nanofibers has the characteristics of simple equipment and easy operation, and is one of the most important methods for preparing polymer continuous nanofibers.
Electrospinning
A schematic diagram of an electrospinning device is shown in Figure 1. It consists mainly of three parts: a high voltage power supply, a spinneret and a fiber collection device. DC power is generally used to supply high voltage power instead of AC power. The high voltage required for electrospinning is 1 to 30 kV. A syringe (or pipette) delivers the solution or melt to the spinneret at its end. The spinneret is a very thin metal tube with electrodes. The collection device or the receiving plate is used to collect the nanofibers, and the arrangement of the nanofibers can be adjusted by changing the geometry and shape of the collecting device.
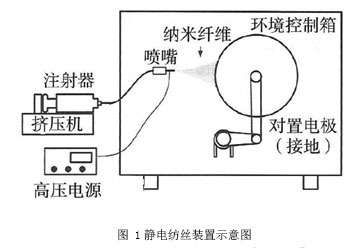
2. Principle of electrospinning technology
As early as 1882, Raleigh's research found that charged droplets are unstable in the electric field. After entering the electric field, they are easily split into smaller droplets due to the electric field force. Taylor's research shows that after the charged droplets enter the electric field through the spinneret, the droplets are gradually elongated under the action of the electric field force and the surface tension of the liquid to form a cone (Taylor cone) and determine its angle. It is 49.3°.
During the electrospinning process, the polymer solution or melt is extruded to the spinneret. Due to the electric field force and surface tension, a Taylor cone is formed at the spinneret, and as the spinning solution is continuously pushed into the electric field, The spinning solution is ejected from the tip of the Taylor cone and is continuously stretched by the electric field force in the electric field. When the jet is stretched to a certain extent, the surface tension is overcome, and the unstable bending occurs and then pulled. Stretching and splitting into a finer jet, the specific surface area of ​​the jet is rapidly increased to rapidly evaporate the solvent, and finally collected and solidified on a collecting device to form a nonwoven fabric-like fiber mat.
3. Influencing factors of electrospinning
The factors affecting electrospinning mainly include solution properties (such as viscosity, concentration, relative molecular mass distribution, elastic conductivity, dielectric constant, surface tension, etc.), process conditions (such as voltage, extrusion rate, spinneret and receiver). The distance between them, the diameter of the spinneret, etc.) and environmental factors (such as temperature, humidity, gas flow rate, etc.). Many people have conducted research on this aspect.
The existing research results show that in the electrospinning process, the main process parameters affecting fiber properties are: polymer solution concentration, spinning voltage, curing distance (nozzle to wire device distance), solvent volatility and extrusion Speed, etc.
(1) concentration of the solution solution
The higher the concentration of the polymer solution, the greater the viscosity and the greater the surface tension, and the ability of the droplet to split after exiting the nozzle decreases as the surface tension increases. Generally, when the other conditions are constant, the diameter of the fiber increases as the concentration of the polymer solution increases.
(2) Spinning voltage
As the voltage applied to the polymer solution increases, the electrostatic force of the system increases, the splitting ability of the droplets increases accordingly, and the diameter of the resulting fibers tends to decrease.
(3) Curing distance
After the polymer droplets are ejected through the nozzle, the compound is concentrated and solidified into fibers in the air while being accompanied by the solvent volatilization, and finally accepted by the wire receiving device. For different systems, the effect of curing distance on fiber diameter is different. For example, studies on polystyrene (PS)/tetrahydrofuran (THF) systems have shown that changing the cure distance has little effect on fiber diameter. For polyacrylonitrile (PAN)/N,N-dimethylformamide (DMF) systems, the fiber diameter decreases as the receiving distance increases.
(4) Solvent
Similar to conventional solution spinning, the nature of the solvent has a large effect on the formation, structure and properties of the solution electrospun fibers, and the volatility of the solvent plays an important role in the morphology of the fibers.
4 application of electrospinning technology
With the development of nanotechnology, electrospinning, as a simple and effective new processing technology for producing nanofibers, will play a huge role in biomedical materials, filtration and protection, catalysis, energy, optoelectronics, food engineering, cosmetics and other fields. .
1 In the field of biomedicine, the diameter of nanofibers is smaller than that of cells, which can simulate the structure and biological function of natural extracellular matrix; most tissues and organs of humans are similar in form and structure to nanofibers, which are used for tissue of nanofibers. And the repair of organs provides the possibility; some electrospun raw materials have good biocompatibility and degradability, can enter the human body as a carrier, and are easily absorbed; in addition, electrospun nanofibers have large specific surface area and porosity. Such excellent characteristics, therefore, it has attracted the attention of researchers in the field of biomedicine, and has been well applied in drug controlled release, wound repair, biological tissue engineering and so on.
2 The filtration efficiency of the fiber filter material increases as the fiber diameter decreases. Therefore, reducing the fiber diameter becomes an effective method for improving the filtration performance of the fiber filter material. In addition to its small diameter, electrospun fibers have the advantages of small pore size, high porosity, and good fiber uniformity, which make it have great application potential in the fields of gas filtration, liquid filtration and personal protection.
3 Electrospun fibers can effectively regulate the fine structure of fibers, combined with low surface energy materials, can obtain materials with super hydrophobic properties, and are expected to be applied to the outer shell of ships, the inner wall of oil pipelines, high-rise glass, automotive glass and so on. However, in order to realize the application in the above self-cleaning field, the electrospun fiber material must be improved in strength, wear resistance, and the bonding fastness of the fiber membrane material to the matrix material.
4 The catalyst particles with nanostructures are easy to agglomerate, thereby affecting the dispersibility and utilization rate. Therefore, the electrospun fiber material can be used as a template to uniformly disperse, and at the same time, the flexibility and ease of operation of the polymer carrier can be exerted. It is also possible to utilize a surface composite of a catalytic material and a polymer micro-nano size to generate a strong synergistic effect and improve catalytic efficiency.
5 Electrospun nanofibers have a high specific surface area and porosity, which can increase the area of ​​interaction between the sensing material and the detected object, and is expected to greatly improve the performance of the sensor. In addition, electrospun nanofibers can also be used in energy, optoelectronics, food engineering and other fields.
5Technical progress of electrospinning
5.1 Technical improvement of electrospinning
(1) Common electrospinning
In 2003, the University of Phillips in Germany developed a common electrospinning technology with Zassman of Israel. This spinning technique has two solutions using two nozzles. A composite droplet is formed at the front end of the nozzle to generate a jet, and the inner droplet also enters the jet. Therefore, droplet control is difficult. If it is well controlled, it becomes a core-shell structure, and hollow fibers can also be produced using this method.
(2) Development of TUFT
TUFT is an abbreviation for tubular fiber template. It is made of polymer to make nanofibers, so that other polymers, metals, ceramics, etc. are adsorbed on the nanofibers, and then the original polymer is removed, and the middle becomes hollow. It is also possible to form a composite layer to produce a nanocapacitor. For example, if a polymer is added to the outside of the palladium particles, a nanocable having an inner conductor and an outer insulator layer can be obtained. If aluminum is attached to the polymer, an alumina tube can be obtained; by attaching the chromium to the polymer, a chromium tube is obtained.
(3) Compound nozzle
Electrospinning is basically a nozzle method, and Japan's Shiga Prefectural University has developed a composite nozzle. In order to continuously manufacture nanofiber nonwoven fabrics, composite nozzles are indispensable. Since the intervals of the upper, lower, left, and right sides of the nozzles are large, the influence of electrostatic repulsion becomes small. Therefore, the nozzles are generally arranged at intervals of 10 mm left and right, and 50 mm above and below. The nozzle is made of a stainless steel tube having an inner diameter of 0.5 mm, and a solution is delivered to each of the steel tubes using a fluororubber tube having good chemical resistance. Each stainless steel tube is inserted into a hole opened in the copper tube, and a high voltage is applied to the copper tube. To this end, the stainless steel tube is fixed to the extent that it is in firm contact with the copper tube, but can be removed. The nozzles now in use are in a linear arrangement.
5.2 Development of M-ESP
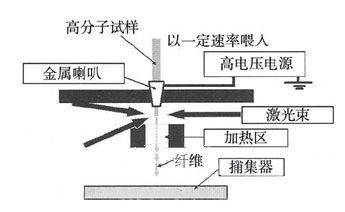
F. Ko et al. grounded the nozzle of the extruder, applied a high voltage to the trap (fiber receiver), and electrospun polypropylene (PP), but the fiber having an average diameter of 1 μm or less was not obtained using the apparatus. Moreover, the fibers collected on the trap cannot be taken out under high voltage application, and there are industrial application problems. Warner winds the PP-filled syringe with a plastic tube, in which the heat carrier is circulated to form a melt, the spinning space is placed in a heated state, and a high voltage is applied between the nozzle on the mounting syringe and the trap, first Nanofibers were obtained. Joo et al. added polylactic acid (PLA) to the syringe to manufacture a device capable of controlling the temperature of the syringe, the spinning temperature, and the temperature of the trap, and successfully manufactured the PLA nanofiber. The apparatus used in the above study was to produce a polymer melt in a container, and a nozzle was provided on a part of the container. This is just to replace the polymer solution with a melt on the S-ESP. This method can also be said to be an extension of the S-ESP.
Fukui University of Japan has developed a device that irradiates a polymer rod from a distant place with a laser beam, and a part of it is produced into a melt, and a high voltage is applied to the melt. The principle of operation of the device is to supply a polymer rod material (about 1 mm in diameter) to the melting portion at a constant speed (about 0.2 mm/s), and simultaneously heat the front end of the polymer rod in three directions with a carbon dioxide laser to locally homogenize the polymer rod. Melting, and applying a high voltage to the polymer melt, the fibers are produced by electrostatic traction in a heated state in the spinning space. The laser-irradiated portion has a spindle shape, and one fiber is formed from the lower portion thereof (Fig. 2).
As a result of trial production of various polymer fibers, it was revealed that only one fiber was formed from the molten portion, and the fibers collected on the trap had an average diameter of 1 μm or less. The device is characterized in that local heating is instantaneously performed by laser heating, and energy loss is small; since it is indirect heating, the device is not required to be high; since the spinneret is not used, the slice having a high melting point can be spun.
6 Conclusion
At present, electrospun nanofiber technology is still in the early stage of development, but it has already seen its broad application prospects, and it will create hundreds of millions of market value in the future. Researchers will also overcome the technical difficulties in the field of nanofiber applications, and perhaps each technology can drive the technological advancement of the entire textile industry. Of course, advances in these technologies require close cooperation in all areas of society, such as textile technology, chemical technology, biology, polymer science, and materials science.
Domestic high-tech enterprise Foshan Lezi Precision Measurement and Control Technology Co., Ltd.
NINGBO BRIGHT MAX CO., LTD. , https://www.brightmax-equine.com