BAIDU_CLB_fillSlot("858283");
At present, corrugated cardboard liners are widely used in automobile spare parts cushioning packaging structures. They can be designed with ingenious structure, use a minimum amount of material to exert a large buffer protection effect, and even help to strengthen the compressive strength of corrugated boxes. . The corrugated cardboard liner can be die-cut, easy to mass-produce, low in cost, and fully recyclable. It is a cushioning material with excellent comprehensive performance. The gasket made of corrugated cardboard mainly has the following structures.
Insert spacer
The gaskets used in the assembly and packaging structure of automobile spare parts are plug-in gaskets. The main function is to layer and isolate the inner space of the corrugated box to form a regular small chamber to avoid mutual A cargo damage occurred in the collision. Generally, multi-layer or left-right separation needs to be assisted by a single piece of corrugated cardboard. It can be used to package irregularly shaped parts. It is convenient to load and unload, has a large number of packages, low packaging cost, and can be recycled. Figure 4 shows the structure of a corrugated cardboard insert liner and its application in the assembly of automotive spare parts.
Folding pad
Corrugated cardboard folding liner can be used as the inner packaging cushion for single-product automotive spare parts. It has various structural forms and can be fixed, shockproof and cushioned after molding. Corrugated cardboard folding gaskets are mainly used for automotive spare parts that do not require particularly high cushioning performance or relatively low shipments.
Cascading pad
Laminated gaskets are suitable for heavy-duty automotive spare parts. These liners are mainly used to interlace corrugated paperboard or laminate them into a cardboard stacking material in parallel, and then cut along the vertical direction of the twisting direction to make the corrugated cardboard section appear honeycomb. The shape is then indented and chamfered so as to be folded into various cushioning members, or cut into cushioning sheets of various groove shapes or cross sections. The stacked gaskets with the above processing methods have many advantages, such as non-polluting materials, recyclable materials, meeting the requirements of light weight, certain fixing and cushioning properties, and optimization of size and performance.
It is worth noting that the cross-section of the laminated gasket is relatively hard. When packaging automotive spare parts with anti-scratch requirements, it is necessary to use materials such as plastic bags with better surface protection.
Corrugated board combined with cushioning material
(1) Corrugated board and pearl cotton combination
EPE is a kind of polymer foam plastic, and it is also a cushioning packaging material with low comprehensive density, semi-rigid, non-toxic, corrosion-resistant, water-blocking and easy recycling. EPE has the advantages of good splicing processing performance, high tensile strength, good cushioning performance, resistance to multiple impacts, small dynamic deformation, and good antistatic performance. It is suitable for automobile spare parts which are more expensive, brittle and have high requirements on cushioning performance. .
Because pearl cotton has the disadvantages of relatively high cost, poor rigidity, and inability to mold, there are not many types of automobile spare parts suitable for single products, but when combined with corrugated cardboard, it can form a cushion structure with ideal cushioning performance. Reduce the use of pearl cotton while ensuring the safety of automotive spare parts. This combined cushioning structure can also achieve packaging cost savings while improving the overall packaging effect.
(2) Corrugated board and honeycomb paperboard combination
For some high-quality, high-quality automotive spare parts, such as car engines, gearboxes, etc., usually plywood boxes are used for packaging, sometimes with a large amount of filler for fixing and buffering, or the combination of EVA materials and wood boards. Bit mode acts as a buffer, but these practices are less than ideal and costly. Through the improvement and optimization, a Sino-US joint venture automobile production enterprise introduced a buffer packaging design scheme combining corrugated cardboard and honeycomb paperboard, which effectively reduced the packaging production cost and obtained a good application effect.
The advantages and disadvantages of honeycomb paperboard and corrugated paperboard are similar. The flat compressive strength of honeycomb paperboard is 5~10 times of the flat compressive strength of ordinary corrugated paperboard, but its cushioning performance in the vertical direction is not as good as corrugated paperboard, and the production efficiency and cost performance are not as good. Corrugated cardboard has not been promoted in the packaging of automobile spare parts. At present, it is mainly combined with corrugated cardboard to make cushioning cushions, so that the respective advantages of corrugated cardboard and honeycomb paperboard can be integrated, and the cushioning performance and compressive strength of the cushion can be improved.
The above content is reproduced in the "Printing Technology" official WeChat (Printech1957), authorized by the company to publish, copyright, piracy will be investigated!
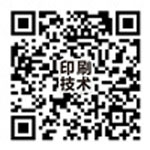
LCD Hair Dryer,Digital Hair Dryers,lcd display hair dryer,Hair Dryers
Zhejiang Hisun Electrical Appliance Co.,Ltd , https://www.cn-hisun.com